Insights
How Prodigy Can Help You Turn a Proof-of-Concept Electrical Prototype Into a Production-Ready Device
Designing and building a proof-of-concept electrical prototype is a monumental achievement to be sure. But the next stage of the journey—from prototype to production—is a lot more complicated and perilous.
For example, imagine that you have designed an Arduino or Raspberry Pi-powered proof-of-concept electrical prototype. It’s now running flawlessly and you want to get it into production with its own printed circuit board (PCB). How do you minimize the chances of supply-chain interruptions getting in the way of future production? How do you maximize quality while maintaining a competitive price point?
If you’ve never gone from prototype to production before, the process can be formidable. Fortunately, the electrical engineers and programmers at Prodigy have developed a nine-step formula for transforming electrical prototypes into production-ready devices.
Here are the nine steps we use to ensure success for our clients:
1. Create a set of requirements
Every prototype-to-production project needs to begin with a list of requirements. Requirements are essentially a way of communicating to the electrical engineer what you want the device to do, how well it has to perform, and your customers’ expectations for the device. This information is critical to the success of the project.
Examples of requirements include operating voltage, speed at which the product must execute commands, environmental conditions, and interfaces to other devices. Prodigy can help you develop these along with other requirements you may not have even considered.
2. Select key electrical components.
After completing the requirements, it’s time to select key electrical components. These could include a microprocessor, power supply, display, sensors, switches, actuators, or motors needed to allow interaction with the product.
Prodigy has experience with many families of microprocessors and other components. This will make the entire component selection process structured and methodical.
3. Create a schematic.
A schematic is essentially a roadmap that the electrical engineer creates to develop the design of the circuits to place on the PCB. The engineer documents all electrical components in the schematic and creates the connections needed for the circuit. At this point, the engineer may also complete various calculations as required. For example, a power budget may be needed to document the amount of power needed to drive different parts of the circuit. These calculations are particularly important for checking whether secondary electrical components—such as resistors and capacitors for example—are properly sized to handle the power within the circuit.
The schematic design software also generates the BOM for the PCB assembly. The contract manufacturer or OEM will use the BOM to control what components are placed and soldered on the board during assembly.
4. Create a PCB layout.
With the schematic behind us, we can now begin developing the PCB. This is typically called the layout process. The layout documents the locations of all the electrical components and the copper traces needed to connect the components and create the circuit.
The layout is not just an electrical task. It also involves input from a mechanical engineer who may have limited space requirements for fitting the PCB, in addition to specific methods for mounting. The electrical engineer has to balance the mechanical needs with the electrical needs of the circuit—so all the mechanical and electrical requirements are met.
The engineer creates the PCB layout in software like PADs,Altium, OrCAD, and Eagle. Prodigy’s staff is fully trained and experienced in these software programs as well as lesser-known programs that generate layouts.
5. Build a prototype PCB.
The engineer uses the PCB layout to generate the files needed for a printed circuit board manufacturer to produce the PCB. These files are typically called Gerber format files and are the industry standard for creating a PCB from a layout. Depending on the size of the board and complexity, completing a prototype PCB requires as little as 2 weeks.
6. Assemble the PCB.
With board in hand, it is now time to solder the electrical components called out in the schematic to the board. This is where the Prodigy electrical engineers really deliver. We have assembled hundreds of boards over the years—some with over 5000 components. When assembly is complete, each board undergoes a detailed inspection and runs through a rigorous power up test (also called bring up test) to make sure the board is functioning properly and ready to go.
7. Firmware development.
The Arduino or Raspberry Pi program for the proof-of-concept prototype may not be able to be run directly on your newly assembled PCB. Either that, or it could be difficult for the contract manufacturer to program. In this case, the microprocessors used in your board will require new code or firmware—written in either C or C++. The Arduino or Raspberry Pi program will be useful in this development as a reference since it contains the basic functionality that you required in the proof-of-concept prototype.
Prodigy has successfully written hundreds of firmware programs for new PCB’s. These days, many of our clients are finding it increasingly necessary to modify their existing PCB firmware due to supply chain issues with components like microprocessors.
8. Testing and revisions.
As a key part of the requirements creation process at the beginning of the project (Step 1 above), Prodigy engineers outlined a test plan/procedure. We will now initiate that test procedure on the assembled PCB with the new firmware installed. The engineer will review the test results for issues that could require revisions to the PCB or the firmware to improve performance. This is also the time to address scope changes that may have occurred during the PCB development process.
9. Release and production.
After testing any revisions—and you are satisfied with the product’s performance—Prodigy will then generate a package of production documents that the contract manufacturers can use to provide a quote and ultimately start production. Prodigy even offers support to help select a contract manufacturer and answer questions your suppliers may have about substitute components and other technical issues.
Final Thoughts
We know that the prototype to production process can feel daunting and overwhelming—especially because you want your final product to be just as well-formed and well-polished as the prototype (if not more so).
However, if you follow the process detailed above, we are certain that it will maximize your chances of success. In fact, Prodigy has taken hundreds of proof-of-concept prototypes through the above nine-step strategy to successfully create production PCBs for our clients. We can do the same for you. Give us a call!
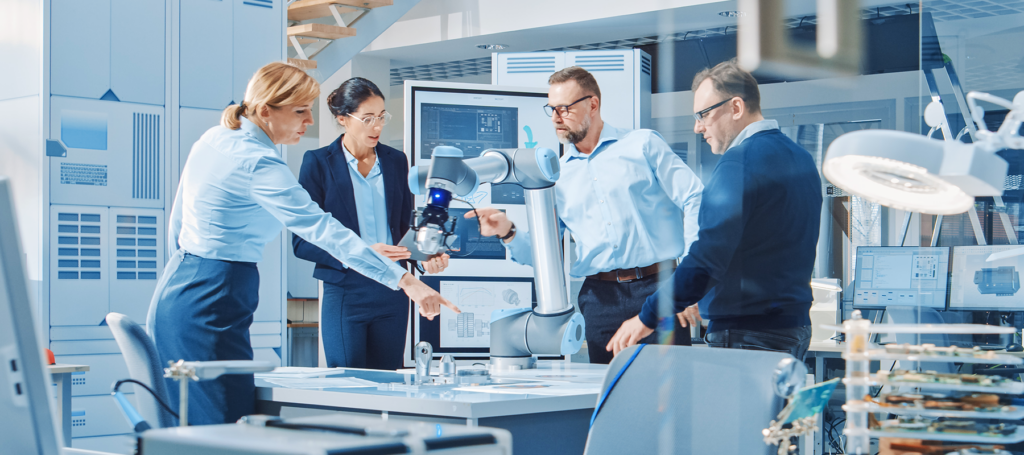
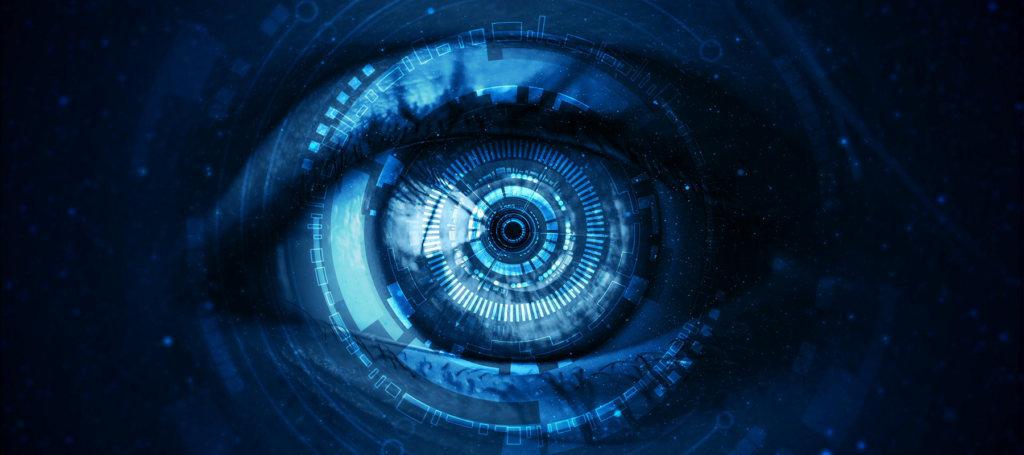