Insights
Medical Device Design Trends for 2022
The Prodigy team has participated in the design and development of a number of medical devices in recent years, ranging from capital equipment to single-use. We’ve learned a lot from our experiences—especially during and after the pandemic. In fact, the pandemic highlighted several key medical device design trends that every product developer needs to consider at this time.
In this article, we explore the three most important medical device design trends for 2022 as they relate to:
- Supply Chain Uncertainty
- Design for Additive Manufacturing
- Simulation and Analysis
Although the medical device design trends in this article came about as a result of pandemic-related challenges, they have also led to exciting innovations and process improvements for the entire product design field.
1. Supply Chain Uncertainty
In the post-pandemic world, supply chain challenges have become the norm. For example, certain materials—such as chips and processors—are difficult to obtain because of COVID-related labor shortages, supply chain difficulties, and geopolitical factors like the war in Ukraine. Due to these serious concerns, it’s important to ask the following when creating a new medical device:
“Does my design have a Plan B or a Plan C if I can’t source a critical, difficult-to-find component? How will I react if the component is suddenly unavailable.”
For some medical equipment projects, answering these questions is easy. All they require is the re-sourcing of components or redesign of boards to accept alternative chips or components. Other projects are inherently riskier because they require a unique component that is extremely difficult to source.
To make sure you’re fully prepared for any supply chain uncertainties, consider the following strategies:
- Determine whether the resurgence of COVID or another pandemic could affect your ability to source parts, components, and supplies—or cause inspection delays.
- Determine the kind of chips that the device requires, how difficult are they to source, and whether you can change the design to use an easier-to-source chip or processor.
- Identify all logistics considerations that could impede the manufacturing process and the delivery of the finished product.
- Consider whether any geopolitical factors might impede the sourcing of components.
In some cases, designing for additive is an excellent strategy for overcoming supply chain uncertainty.
2. Design for Additive Manufacturing Innovations
When components are difficult to source, designing for additive could be a workaround. 3D printing is not just for prototyping anymore. New 3D printing technologies—including industrial applications—are revolutionizing the process of designing new products.
At Prodigy, we have found the additive manufacturing process feasible for certain medical device design situations—allowing us to ship a final product or pilot the first release faster. Of course, it is essential to properly vet the situation and compare all options before moving forward with a 3D printing strategy. Also, product designers may want to create a machine-made component for greater efficiency at a later time.
Here are some advantages of the latest design-for-additive technology improvements:
- New 3D printing technology means that design-for-additive costs are decreasing and the technology is more mature for final products.
- New biocompatible materials are currently available for design-for-additive processes.
- Design for additive supports decentralized production, which empowers product designers to overcome sourcing problems. For example, a component produced with additive manufacturing no longer lives with a single supplier—allowing you to source original parts from a number of different suppliers.
- Design for additive also allows product designers to develop and manufacture multi-feature parts that would normally require a combination of multiple manufacturing methods. For example, 3D printing can often allow you to streamline the production process by creating a multi-feature part that doesn’t require multiple manufacturing methods or tooling setups.
The most recent simulation and analysis technologies are particularly suited to design-for-additive activities.
3. Simulation & Analysis Technology Innovations
The latest computer simulation and analysis technology empowers medical device designers to finalize more of their designs before prototyping. This offers greater speed and efficiency—with a substantial reduction in wasted effort and errors—throughout the entire development process.
Here are some of the key benefits that the latest simulation and analysis technologies offer:
- Topology optimization and generative design: Some 3D software can iterate multiple geometries to solve given load cases. This helps designers reduce material use for a structural member, and optimize the structural design or actual geometry for given parameters—such as minimizing deflection with the least amount of material. In many cases, these processes have the added benefit of producing organic, aesthetically pleasing shapes.
- Improved processing power: New simulation and analysis technology offers improved processing power. This makes it easier to use these tools in a design workflow with fewer delays.
- Additive design efficiency: The latest simulation and analysis technology boosts the speed and success of designing a component for additive production.
A Final Thought: Sometimes Design Challenges Bring About Exciting Solutions and Technologies
As you’ve seen in this article, the pandemic may have brought supply chain and component sourcing challenges. However, these challenges have also driven the current medical device design trends in a way that has inspired innovative solutions and technologies related to:
- More resilient and flexible product designs to overcome sourcing challenges;
- The use of new 3D printing design-for-additive technologies that overcome sourcing challenges while allowing product developers to create, manufacture, and ship pilot products faster; and,
- The use of advanced simulation and analysis solutions to improve the speed and efficiency of the entire product design process—while also supporting design for additive.
What medical device design trends have you encountered during and after the pandemic? Please contact us and share your story. The product design engineers at Prodigy would love to hear from you.
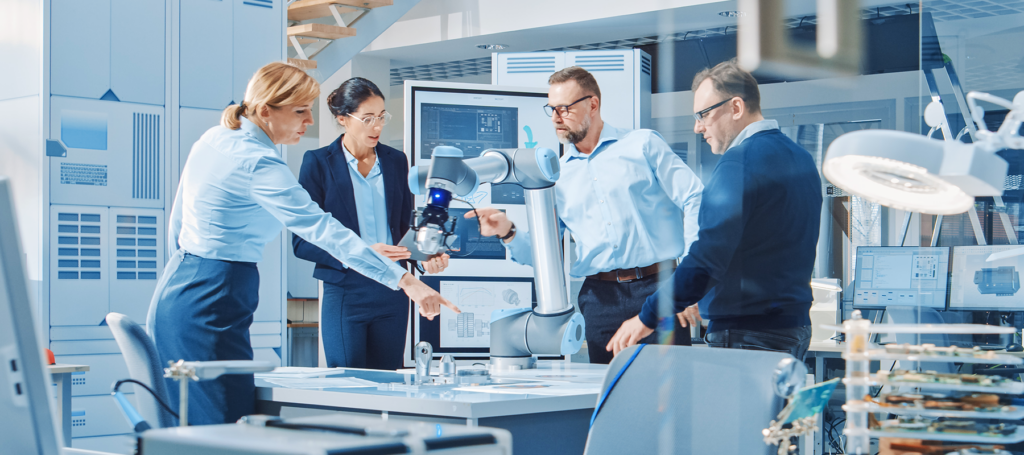
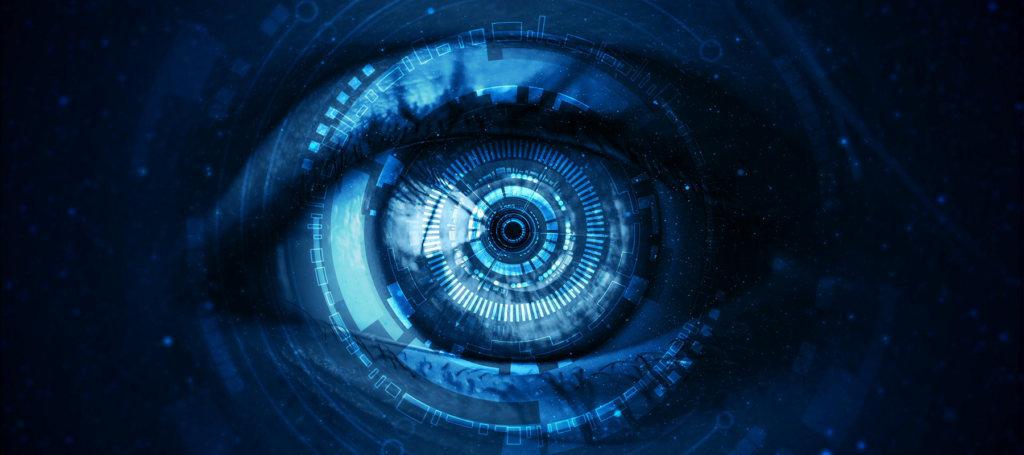