Our Work
SFC Fuel Cell Technology: A Lightweight, Combat-Ready Fuel Cell Design for Remote and Rugged Conditions
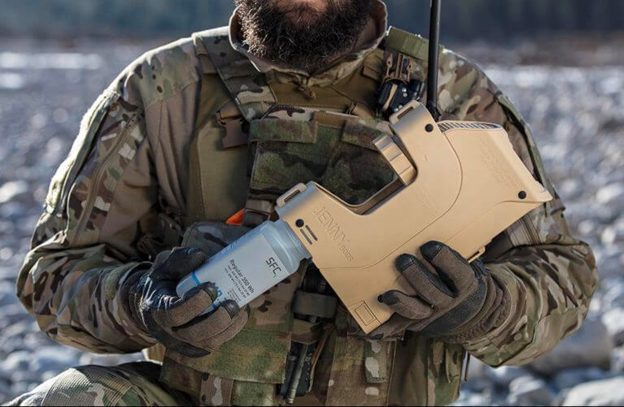
SFC Energy AG is a top provider of methanol and hydrogen fuel cells for both stationary and mobile use cases. They distribute their products to a wide range of customers, including the U.S. military, NATO, the oil and gas industry, and everyday consumers.
In 2008, SFC contracted Prodigy to adapt their portable fuel cell technology to meet the rigorous needs of the U.S. Military and NATO. The primary goals of the project were to design a rugged, compact, and lightweight fuel cell with advanced features for durability, lightness, and stealth in field combat scenarios.
In this case study, we look at how Prodigy achieved the unique goals of this SFC project, which resulted in the successful design of the SFC Jenny series of portable fuel cells for dismounted operations, a product that is still being manufactured and sold to the U.S. Military and NATO today.
Background on SFC Fuel Cells and Prodigy Participation
The SFC Jenny fuel cell project involved the design and development of a portable methanol fuel cell with seven primary goals:
Minimize weight and size: Military personnel carry the Jenny fuel cell in their packs, so a paramount goal of the project was to reduce the size and weight of the device while maximizing durability. At the time, military personnel commonly carried 24.25 lbs (11 kg) of batteries in their packs on average. The aim was to reduce this burden to less than 4 lbs (1.8 kg) with a fuel cell small enough to fit in the side pouch of a backpack.
Ruggedize the unit: The fuel cell needs to survive rough and wet environments, so the durability of the design must endure all terrains—in addition to having shock resistance to protect against drops and falls. It also needs water resistance capacity.
Design for human factors: With many individuals making use of the fuel cell, operating the device has to be intuitive and self-evident, so that anyone can pick up the device and immediately understand how to operate it.
Design a reliable fuel interface: The device relies on a small bottle of liquid methanol fuel which needs to easily attach and detach from the device for refills and replacements. Prodigy had to design a reliable, leak-proof interface for attaching and detaching the bottle.
Address heat dissipation: Because the unit is used in combat scenarios, Prodigy needed to design a system for dissipating heat, to help soldiers and military personnel reduce the chances of detection by enemy heat sensing and infrared technology.
EMI shielding: EMI (Electromagnetic Interference) Shielding is the use of techniques and materials to protect electronic devices from external electromagnetic signals deployed against troops by enemy combatants. EMI shielding is necessary for the SFC Jenny fuel cell to minimize the dangers of enemy-deployed electromagnetic interference.
Design for manufacturability: Last but certainly not least, Prodigy needed to design an easy-to-manufacture fuel cell with easy-to-source parts. In other words, our design had to facilitate and support a reliable manufacturing process for many years to come.
While fuel cell products that meet the above specifications are common today, SFC’s design goals for the Jenny fuel cell series were particularly ambitious in 2008. Since there was nothing like it on the market at the time, our company and its partners worked in an isolated environment for confidentiality purposes during the design and development process.
In all projects we take on, client confidentiality is of utmost importance at Prodigy.
Design Process
To achieve the above design goals, Prodigy formed a team consisting of a project manager, lead mechanical engineer, lead electrical engineer, and lead industrial designer. We also partnered with LPK for the industrial design component.
Prodigy designed a product capable of achieving the outlined goals of the project. Part of the process involved carrying out iterative Computational Fluid Dynamics (CFD) analyses using SolidWorks Flow Simulation to optimize the cooling system for maximum cooling and minimum heat signature detection.
In designing the packaging, Prodigy carried out structural analysis and plastics molding tasks to make the device packaging more robust while harmonizing the ergonomics and practicality of our designs with the initial aesthetics of the industrial design team.
We also improved the stealth capacity of the fuel cell by minimizing its heat signature. This was significant. The Prodigy team iterated extensively on heat dissipation strategies, which now help the fuel cell avoid detection by enemy snipers and infrared sensors.
Finally, soldiers played an important role in a rigorous field testing process. After completing the POC, soldiers tested the device to confirm its durability, functionality, and reliability and to help validate the device to meet the needs of dismounted field operations.
Results
Prodigy engineered the SFC Jenny fuel cell to specification and designed it for immediate manufacturing. This allowed SFC to achieve a successful new product launch and bring the product to market on time and on spec.
In addition to meeting all of the ambitious design goals for the SFC Jenny, the fuel cell’s lightweight and durable construction were particularly admirable. Compared to the 24.25 lbs (11 kg) average weight of batteries that soldiers carry in dismounted field operations, the finalized SFC Jenny fuel cell weighs only 3.75 lbs (1.75 kg) with a full bottle of fuel attached.
As a final indicator of success, the fuel cell is still in use and production today, 15 years after its initial release. The SFC Jenny 6005 and its fuel bottles have NATO supply numbers. Both NATO and the U.S. Military are currently relying on this device to provide energy for military personnel during dismounted field missions and other critical operations.